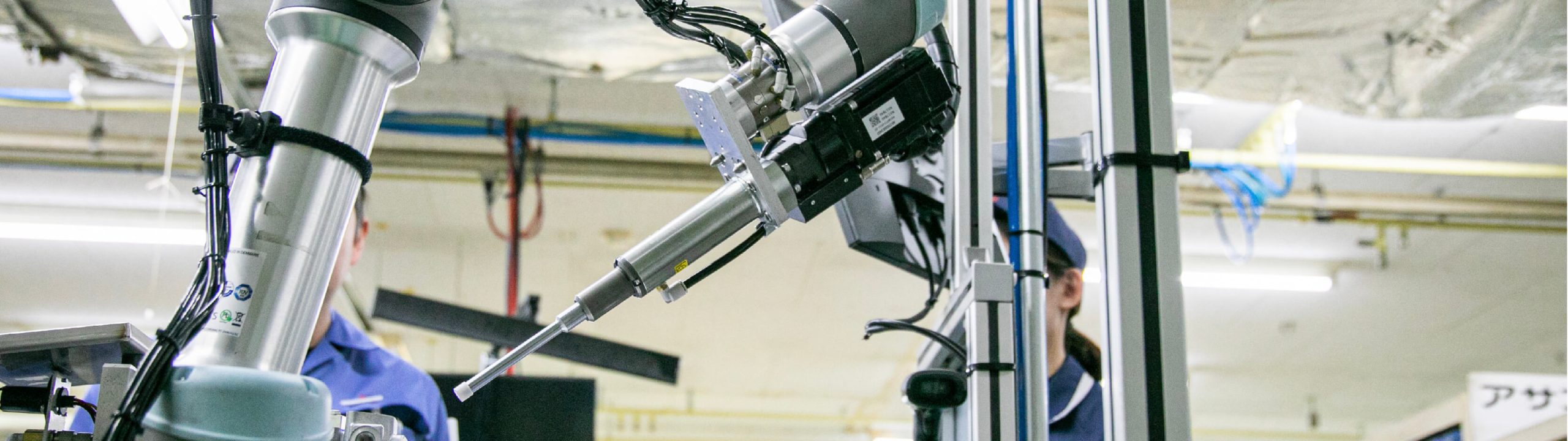
技術開発プロジェクト
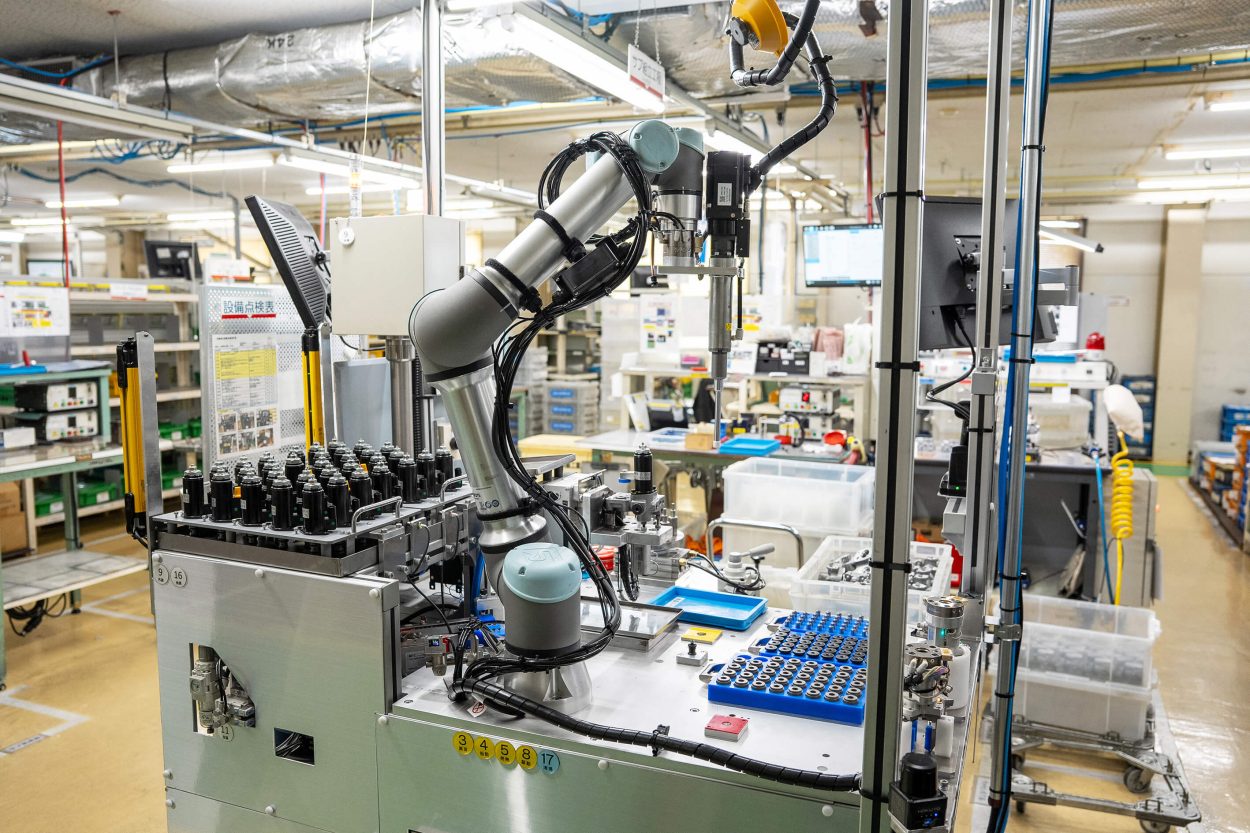
扶桑工業が誇る高度な技術力の背景には、新しいことへの挑戦をいとわない組織風土があります。中でも国産初の手術支援ロボット「hinotori(ヒノトリ)」の部品開発や、人との協働作業を前提とした新たなロボット「協働ロボット」の設計製作は、当社にとって大きな挑戦であり、会社の技術力を大幅に向上させるきっかけとなりました。今回は、この2つのプロジェクトを先導した2人の担当者に、プロジェクトを進める中での苦労と成功までのドラマを聞きました。
世界を支える技術力
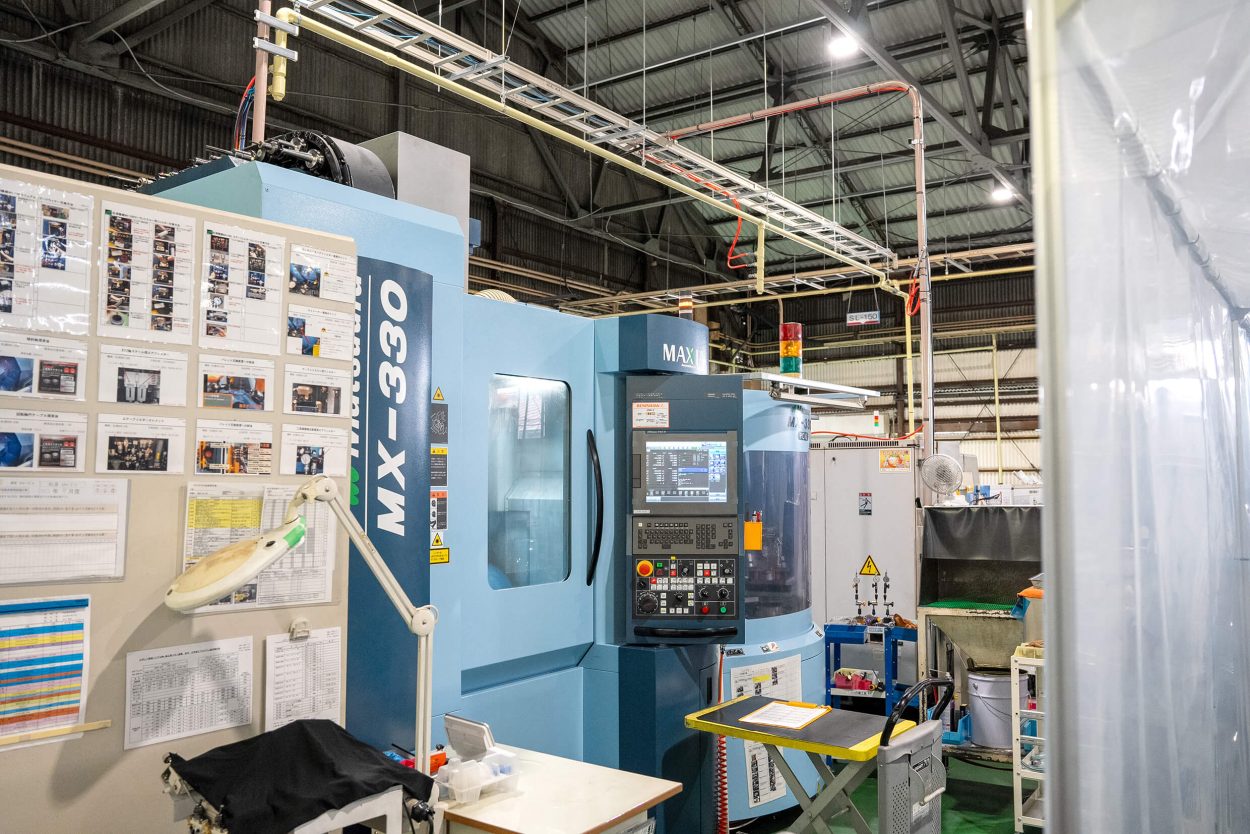
扶桑工業は、滋賀県でも有数の金属加工技術を持つ企業。世界のパワーショベルの約半分に当社のパーツが使われるなど、農業機械や産業機械部品、建設機械部品の分野で世界を支えている。
中でも、金属を溶かし、ダイカストマシンを使って高い圧力をかけながら金型に流し込む量産に優れた加工法「アルミダイキャスト加工技術」においての業界からの評価は高く、薄く、強く、複雑な形の加工までほぼ無欠陥で完成させられるのが当社の強みだ。
扶桑工業が誇る3つの強み
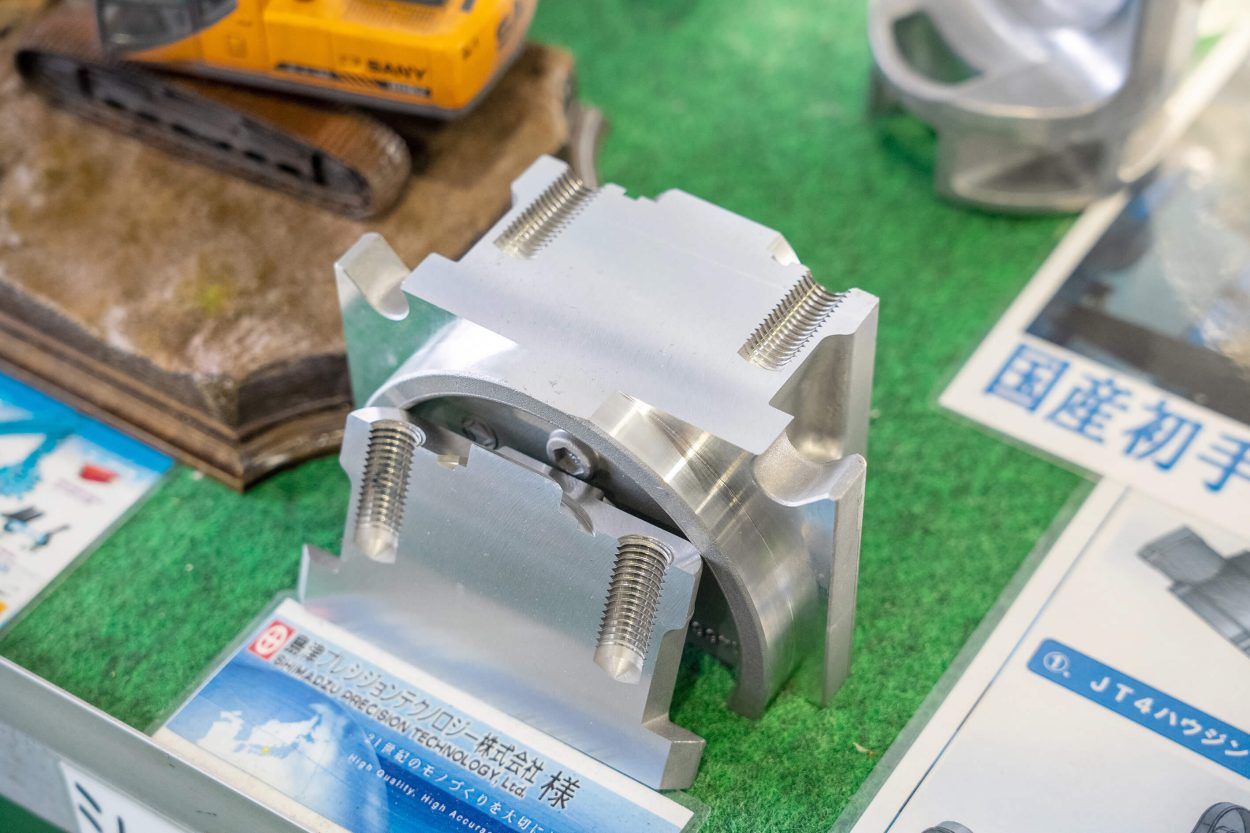
扶桑工業が誇るアルミダイキャストには3つの大きな強みがある。
まずひとつ目は、「局部加圧法」と呼ばれる、製品内に「巣(す)」を発生させない工法だ。高速射出を行うアルミダイキャストでは、ガスの巻き込みで発生する巣をなくすのは困難なのが常識。しかし、巣が発生すると強度が低下する上に、機密部品だとそこから油や空気が漏れるといった不具合が発生してしまう。局部加圧法では、金属が固まる過程で特定の部位を直接加圧することで巣を押し潰す。精密な条件設定を行うことで、厚さ60mmの製品でも巣がない状態で鋳造できるようになった。
ふたつ目は、「PF法」。こちらも製品内に巣を発生させないための工法だが、この工法では金型内の空気を酸素ガスに置き換えることで、酸素ガスが金型に流し込まれたアルミがと瞬間的に化学反応を起こすことで酸化アルミ微粒子となり、理論上、巣のない製品ができるという工法だ。そのための装置自体も自社で開発しており、効率的なプロセスで巣のないダイキャストが作られている。
3つ目は「凝固解析」により品質・効率を高めていること。アルミは薄い部分から固まって、厚い部分ほど固まるのに時間がかかる。冷却が均一に進むよう金型を作る段階でシミュレーションし、冷却する際のレイアウトを工夫することで、より欠陥のない製品作りにつなげることができている。
この3つをバランスよく組み合わせることで、扶桑工業にしかできない高い品質を保つことができている。
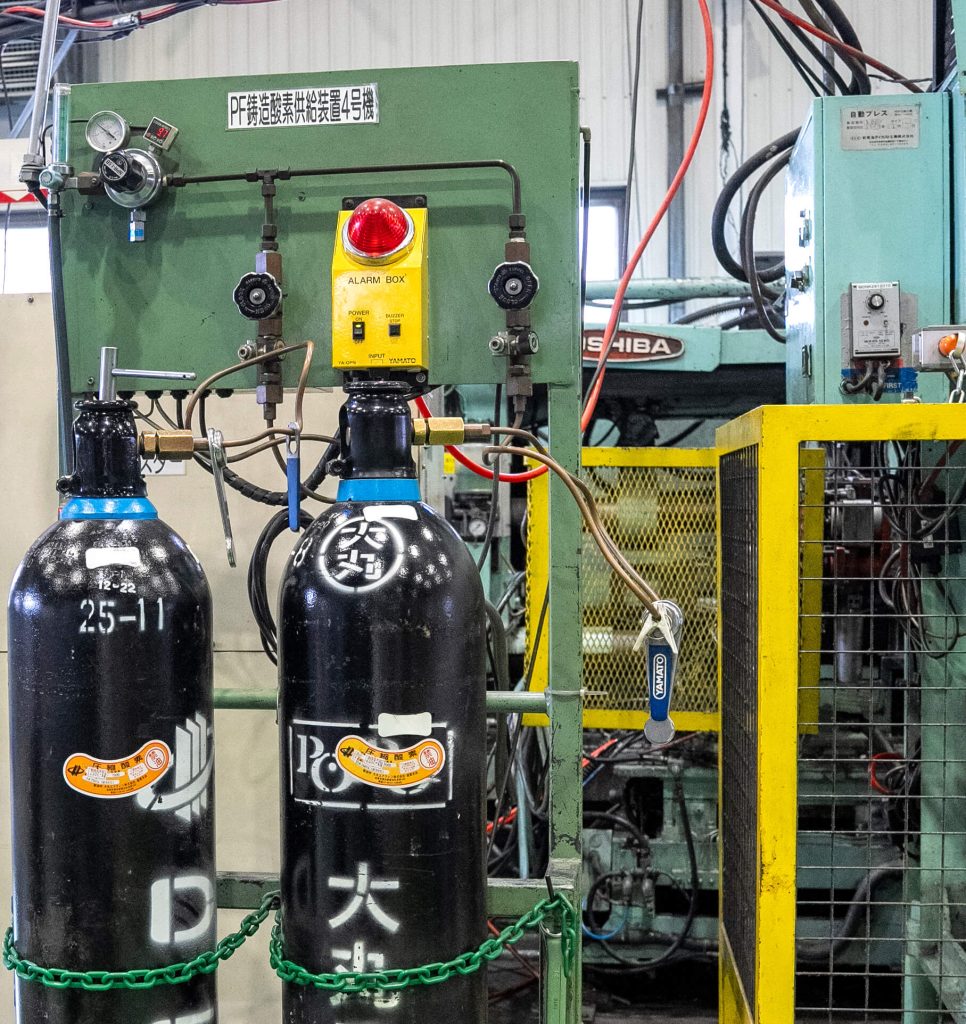
「hinotori」部品開発プロジェクト
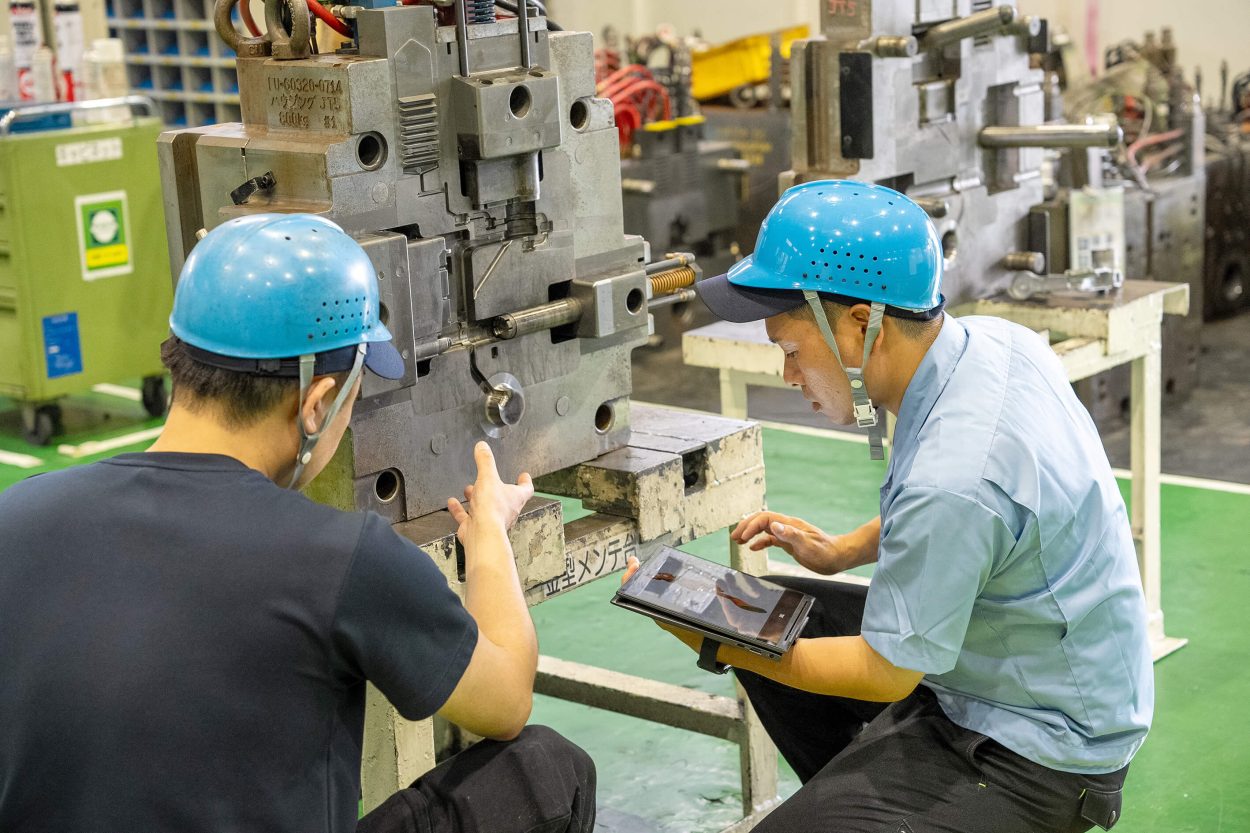
これらの高い技術力がもととなり、社員主体での新規プロジェクトも次々と生まれている。その代表的なものが国産初の手術支援ロボット「hinotori(ヒノトリ)」の部品開発プロジェクトだ。
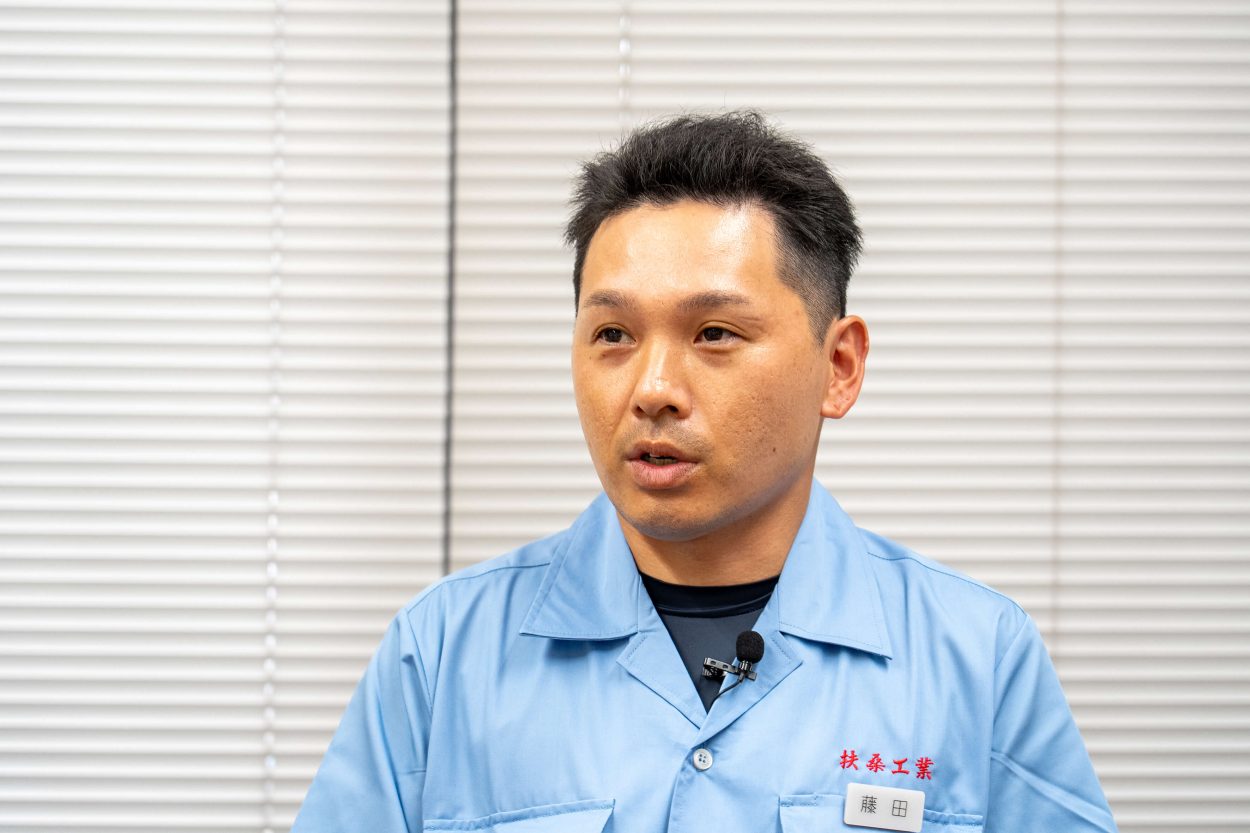
藤田:お客様から新規の見積もり依頼をいただいたのが、プロジェクトが始まったきっかけです。最初はhinotoriの部品ということは伏せられていたのですが、お客様の工場へ行って打ち合わせをしていく中で、日本初の手術支援ロボット部品だと言われて。上司に報告したところ、「すごいじゃないか!」となって2020年11月に「プロジェクトhinotori」としてスタートしました。
始まってからは本当に大変。基本的に金型を1面作るには約3ヶ月かるのですが、今回は金型を8面作って切削加工品の完成品立ち上げまでを6ヶ月でやるという、すごくタイトなスケジュールで。思わず社長に「正気ですか?」っ聞いてしまいました。部品自体もまだ開発段階だったので、お客様と一緒に作り上げていって、結果、半年で完成できた時の達成感はすごかったです。
今は、プロジェクトの立ち上げは完了して量産の方にシフトしています。とはいえまだ不安定要素や課題はあるので、そういう点を少しずつお客様とすり合わせながら試行錯誤と改善を繰り返しているところです。
人と一緒に働く「協働ロボット」の設計製作
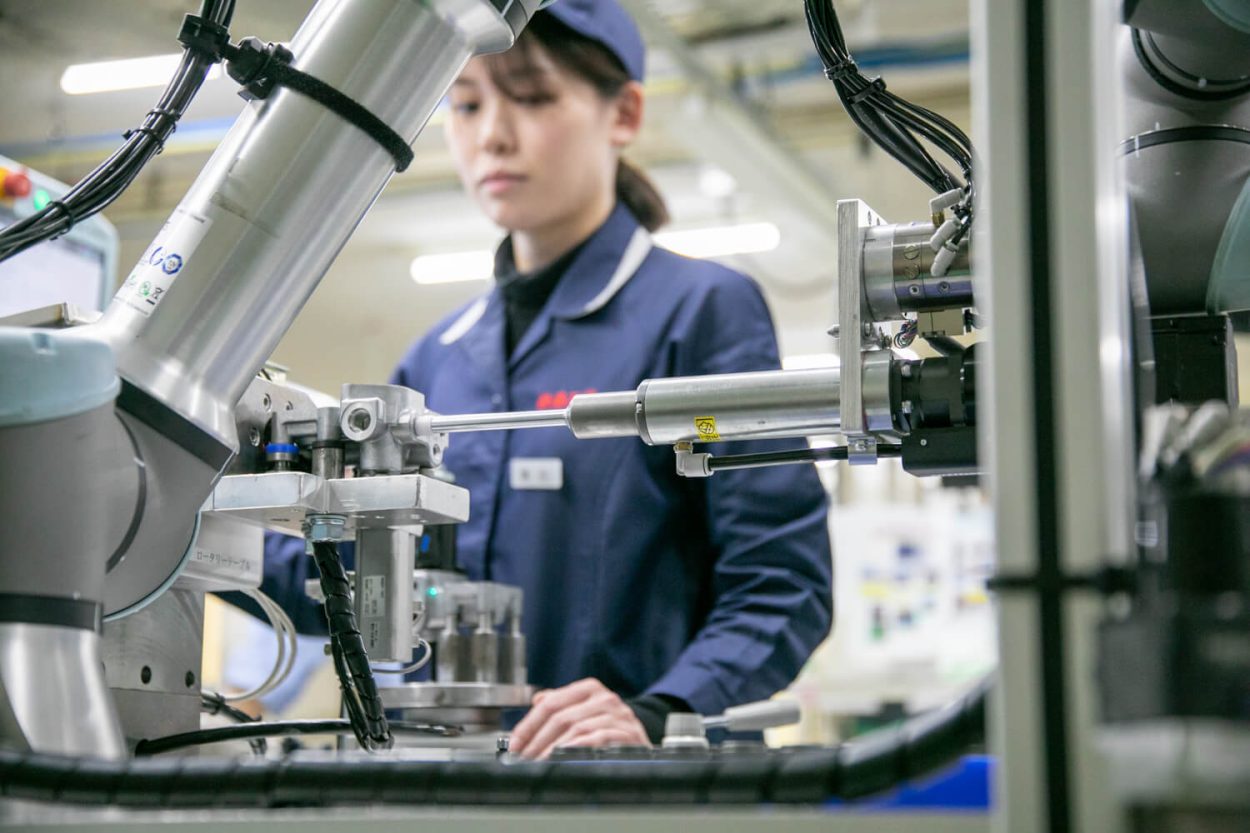
挑戦をいとわない組織風土のベースには、どんな困難も「技術向上のため」という精神が根付いている。その思いは製造に使う装置や設備にも向けられており、「協働ロボット」が生まれるきっかけにもなった。
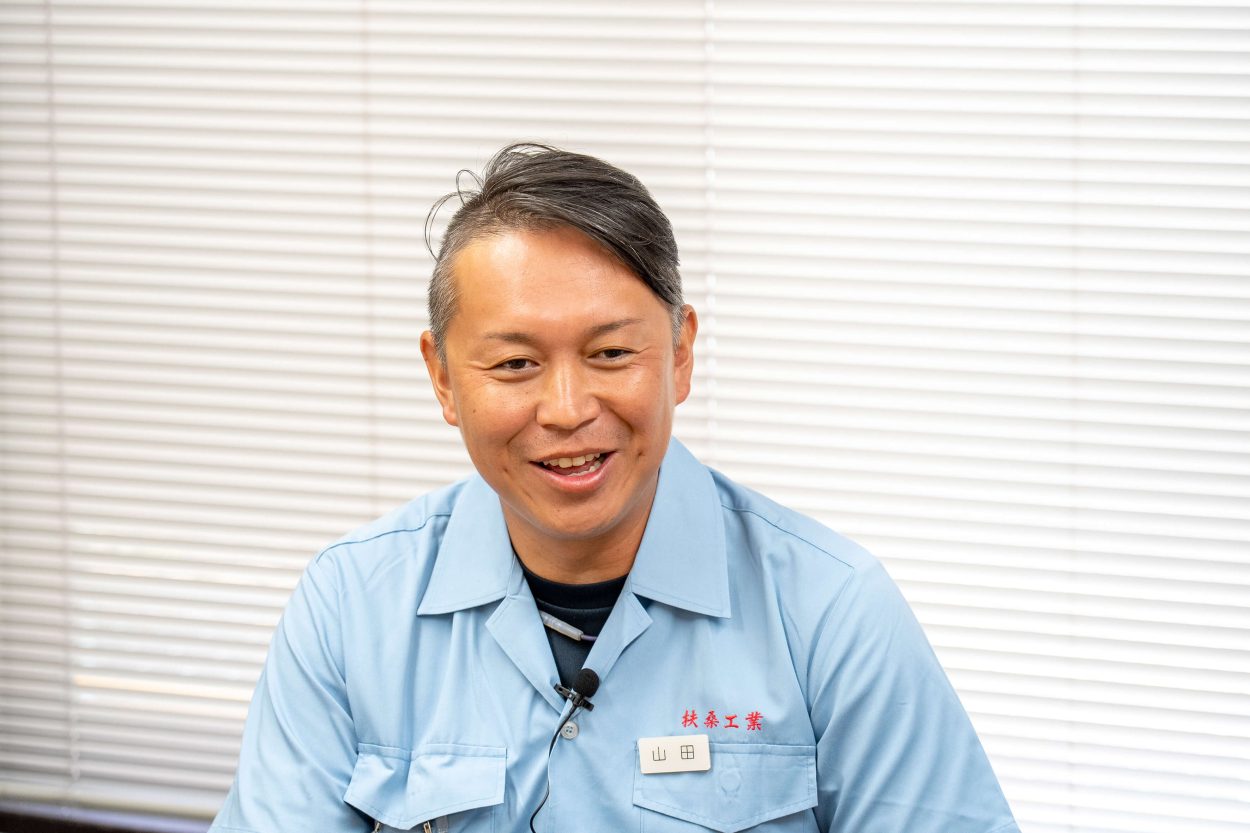
山田:きっかけは、社内の人手不足解消のため。人がやっている作業をロボットに任せて、生産効率を上げるという目的からスタートしました。ロボットには「産業用ロボット」と「協働ロボット」の2種類があって、一般的な産業ロボットは、人とは完全に分離した状況で単純作業を行うのに向いています。安全確保のために柵に囲まれていて、作業中は、人は中に入れません。その一方で技術が進むにつれてロボットの小型化が図られ、人との協働作業を前提としたロボットが出てきました。それが「協働ロボット」です。
今回の設置場所は2階の限られたスペースと決まっていたので、ほぼ選択肢なく協働ロボットを導入することに決まりました。同時に、自社で製作することも。協働ロボットを使用して、自社で作るのは初めてだったので、最初は何もかもが手探り状態。展示会のブースを見学に行ったり資料を集めたり、設計はしたことがなかったので部下に教えてもらいました。失敗とやり直しの連続でしたが、やっと1台完成して、今は現場の社員が生産の動線を確認しながら試運転という形でどんどん動かしているところです。
挑戦の末に得る技術力は、何ものにも代えがたい
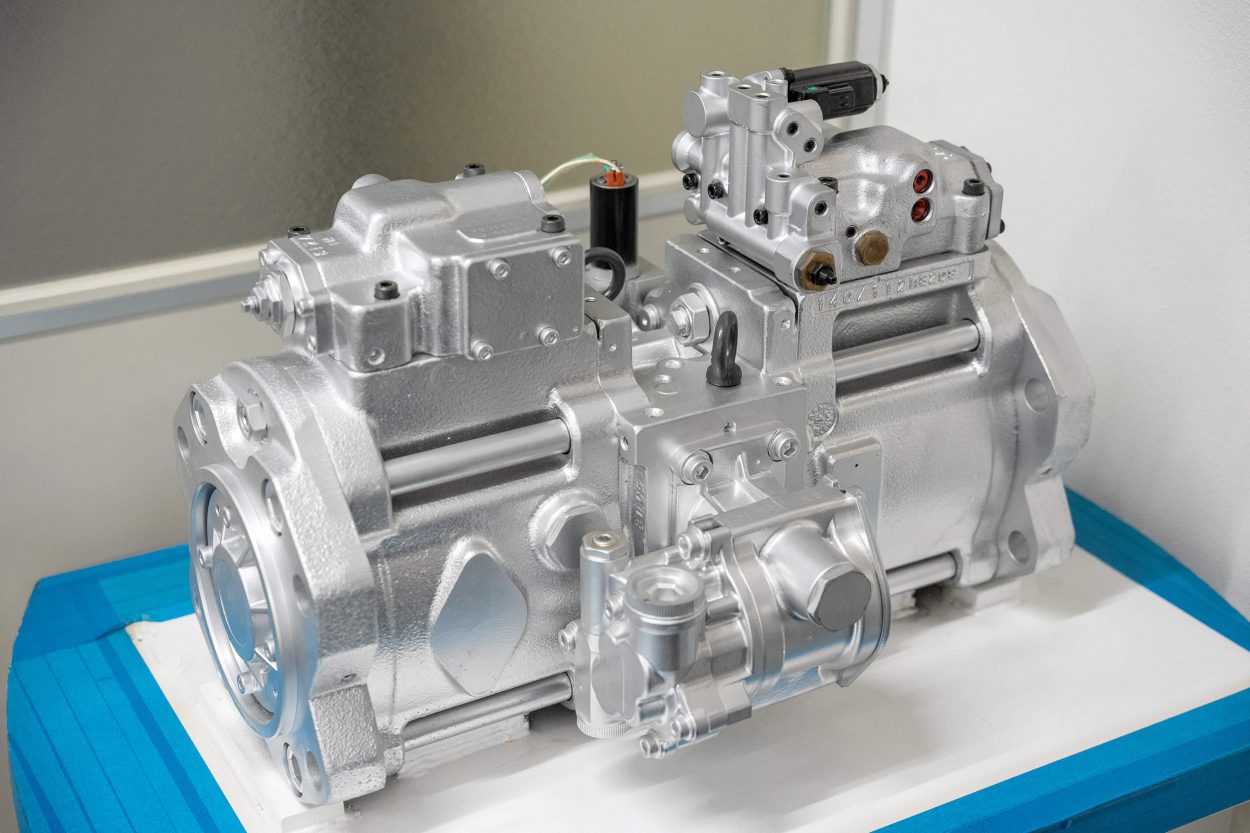
藤田:実は当社は、hinotoriに関わるまでは医療分野にはまったく縁がありませんでした。このプロジェクトが軌道に乗った今、もう一度すぐにでもこれまでとは違う業界に目を向けて、新しいことに挑戦していくべきだと感じています。一緒にプロジェクトを進めてきたメンバーも「今回hinotoriがやれたんだから、もう何が来ても大丈夫!」という気持ちになっているので、これからもっとレベルの高いところを目指していけるのではないでしょうか。
山田:まずは1台目の協働ロボットが完成したので、次はそれを増やして水平展開していくのが目標です。たくさんの製造工程がある工場のラインの中でどこに当てはめると一番役に立つのか、カメラ付けたりITを取り入れたりしてさらにレベルアップしたロボットが作れないか、今は試運転を重ねながら探っているところ。製作中は本当に失敗だらけで、ロボットの傷ひとつ見てもその時の失敗と改善が思い出されます。次に生かせるような経験をたくさんしました。
自社で開発するには手間も時間もかかるが、その後についてくる技術力は何ものにも代えがたい資産になる、と声をそろえて言う2人。これらのプロジェクトには人材育成の目的も含まれており、実際に若手メンバーのスキルアップにも大いにつながったそうだ。挑戦には大きな壁が付きものだが、その壁を壊すでも迂回するでもなく、何とかしてよじ登るのが扶桑流。時代の先を見据えながら、まだ見ぬ未来を思い描く。扶桑工業の挑戦は、これからも続いていく。